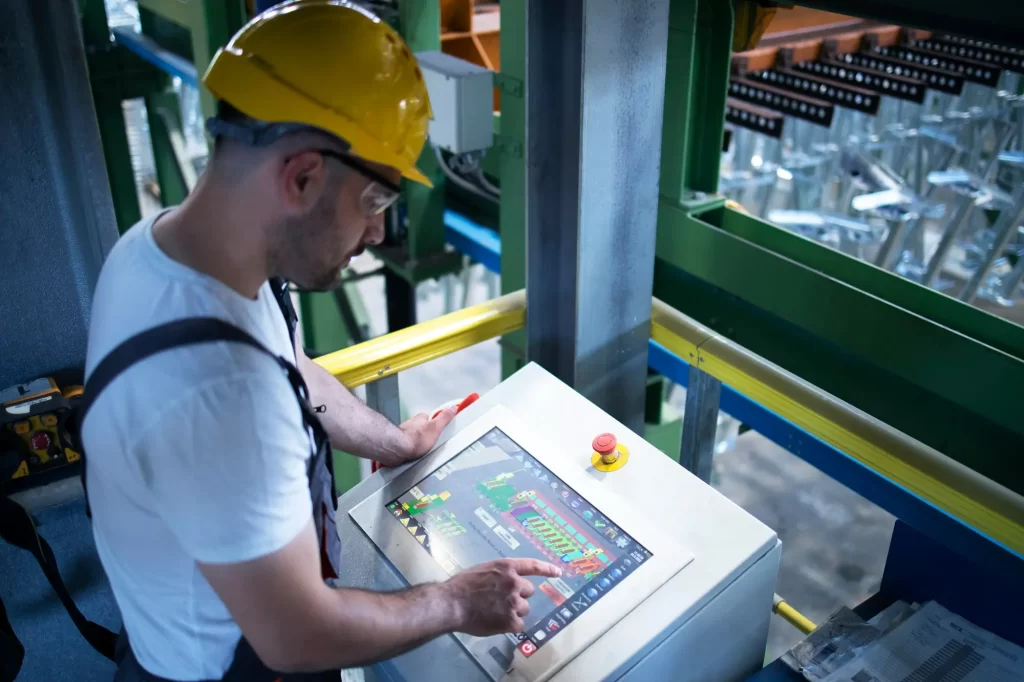
Introduction
The manufacturing sector stands at a critical crossroads where digital adoption is no longer optional but essential for survival and growth. As global competition intensifies and customer expectations evolve, companies that leverage smart technologies gain significant advantages in efficiency, quality, and market responsiveness. This transformation journey, while challenging, offers unprecedented opportunities to reimagine manufacturing operations and establish sustainable competitive advantages in an increasingly digital economy.
What is Digital Transformation in Manufacturing?
Digital transformation in manufacturing represents the integration of advanced technologies into all areas of manufacturing operations, fundamentally changing how organizations operate and deliver value. It’s not merely about technology implementation but involves:
- Comprehensive Process Redesign: Rethinking workflows and operations through a digital lens
- Cultural Shift: Moving toward data-driven decision-making across all levels
- Strategic Realignment: Aligning digital initiatives with core business objectives
- Ecosystem Integration: Creating connected networks across supply chains and stakeholders
Core Technologies Driving Manufacturing Transformation
Internet of Things (IoT)
- Smart Sensors and Devices: Enable real-time monitoring of equipment performance and production metrics
- Connected Factory Floor: Creation of intelligent production environments where machines communicate seamlessly
- Digital Twins: Virtual replicas of physical assets for simulation and optimization
Artificial Intelligence & Machine Learning
- Predictive Analytics: Forecasting maintenance needs, production bottlenecks, and quality issues
- Computer Vision: Automated quality control and defect detection
- Optimization Algorithms: Intelligent production scheduling and resource allocation
Advanced Automation
- Collaborative Robots (Cobots): Working alongside human operators to enhance productivity
- Autonomous Material Handling: Self-driving vehicles for warehouse and factory logistics
- Process Automation: Elimination of repetitive tasks through intelligent systems
Cloud Computing
- Scalable Infrastructure: On-demand computing resources that grow with your needs
- Edge Computing: Processing critical data closer to its source for faster response times
- Software-as-a-Service (SaaS): Specialized manufacturing solutions delivered via cloud platforms
Strategic Benefits of Digital Manufacturing
Operational Excellence
- Reduced Downtime: Through predictive maintenance and real-time monitoring
- Increased Production Throughput: Via optimized processes and reduced bottlenecks
- Decreased Quality Issues: Using AI-powered inspection systems
Financial Performance
- Reduction in Operational Costs: Through automated processes and optimized resource utilization
- Lower Maintenance Expenses: With condition-based and predictive maintenance approaches
- Improved Working Capital: By optimizing inventory and improving forecasting accuracy
Market Competitiveness
- Faster Time-to-Market: With digital product development and flexible production capabilities
- Enhanced Customer Experience: Through product customization and transparency
- New Revenue Streams: From data-driven services and smart connected products
Sustainability Gains
- Energy Consumption Reduction: Through optimized operations and smart energy management
- Decreased Material Waste: Using precision manufacturing techniques
- Reduced Carbon Footprint: From optimized logistics and more efficient processes
Implementation Challenges & Solutions
Organizational Resistance
- Challenge: Employee reluctance to adopt new technologies and processes
- Solution: Structured change management programs focusing on training, communication, and demonstrating clear benefits
Investment Concerns
- Challenge: High upfront costs and uncertain ROI timelines
- Solution: Phased implementation approach starting with high-impact, low-risk projects that demonstrate quick wins
Legacy System Integration
- Challenge: Connecting outdated systems with modern digital platforms
- Solution: Implementing middleware solutions and prioritizing interoperability in technology selection
Cybersecurity Risks
- Challenge: Increased vulnerability due to connected systems
- Solution: Comprehensive security-by-design approaches and regular vulnerability assessments
Skill Gaps
- Challenge: Shortage of digital talent in manufacturing contexts
- Solution: Strategic upskilling programs, partnerships with educational institutions, and selective recruitment
Transformative Use Cases in Manufacturing
Predictive Maintenance
- Implementation: IoT sensors on critical equipment monitoring vibration, temperature, and other parameters
- Impact: Significant reduction in unplanned downtime and decrease in maintenance costs
- Example: A leading automotive manufacturer reduced maintenance costs substantially through predictive algorithms
Real-Time Performance Visualization
- Implementation: Digital dashboards displaying KPIs from production lines in real-time
- Impact: Productivity improvement through faster decision-making and issue resolution
- Example: A consumer goods company achieved notable OEE improvement by implementing real-time analytics dashboards
Autonomous Production Systems
- Implementation: Self-adjusting production lines that modify parameters based on quality feedback
- Impact: Reduction in defects and improvement in throughput
- Example: An electronics manufacturer implemented autonomous quality control, considerably reducing returns
Cloud-Based ERP Integration
- Implementation: Migration from on-premise to cloud-based enterprise systems
- Impact: Faster deployment of new capabilities and reduction in IT maintenance costs
- Example: A mid-sized manufacturer gained real-time visibility across global operations after cloud ERP implementation
AR/VR Applications
- Implementation: Augmented reality guides for assembly and maintenance procedures
- Impact: Reduction in training time and faster maintenance execution
- Example: An aerospace component manufacturer reduced assembly errors using AR-guided workflows
Implementation Roadmap for Manufacturing Leaders
Phase 1: Assessment & Strategy (3-6 Months)
- Conduct digital maturity assessment
- Identify high-impact opportunity areas
- Develop business case and transformation roadmap
- Secure executive sponsorship and resources
Phase 2: Foundation Building (6-12 Months)
- Implement core infrastructure upgrades
- Deploy initial data collection systems
- Conduct pilot projects in high-priority areas
- Develop digital skills and change management protocols
Phase 3: Scaled Implementation (12-24 Months)
- Roll out successful pilots across the organization
- Integrate systems and create unified data platforms
- Implement advanced analytics capabilities
- Refine processes based on initial learnings
Phase 4: Continuous Evolution (Ongoing)
- Explore emerging technologies and new use cases
- Optimize existing digital initiatives
- Develop advanced capabilities in AI and automation
- Foster innovation culture and continuous improvement
Key Takeaways for Manufacturing Executives
- Start Now, Even if Small: Begin with targeted initiatives that demonstrate value and build momentum for broader transformation
- Prioritize Data Foundation: Invest in data infrastructure and governance as the backbone of successful digital initiatives
- Focus on People: Technology alone doesn’t drive transformation—invest equally in skills development and change management
- Build Ecosystem Partnerships: Collaborate with technology providers, startups, and industry peers to accelerate innovation
- Maintain Security Focus: Implement robust cybersecurity measures from the beginning of your transformation journey
- Measure Relentlessly: Establish clear KPIs to track transformation progress and demonstrate value to stakeholders
- Think Long-Term: View digital transformation as a continuous journey rather than a one-time project
The manufacturing leaders who will thrive in the next decade are those who embrace digital transformation not merely as a technology upgrade but as a fundamental reimagining of their business models and operations. By taking a strategic, measured approach to implementation while maintaining a clear vision of the digital future, manufacturers can position themselves at the forefront of the industry’s evolution.